金属加工
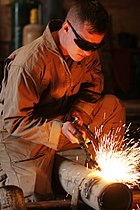


金属加工(きんぞくかこう、英: metal working)とは、金属材料にほどこす加工である。
金属加工は木工(木材加工)や石工(石材加工)などと対比される。
概説
[編集]金属加工には数千年以上の歴史があり、歴史的起源は様々な文化や文明に遡ることができる。金属加工は、太古の昔の金の発見とともに始まった、と考える人もいる。またその歴史は、さまざまな鉱石の精錬法の発見とともに展開したともされており、それで得られるようになった金属という材料の持つ展性や延性などといった特性を活かしつつ、道具や装飾品などに加工してきた歴史である。現代では金属加工というのは、科学でもあり、技能でもあり、また趣味として行われる場合もあれば、産業として行われる場合もある。→#歴史
ひとくちに金属加工と言っても、そのスケールは様々であり、大きなものではたとえば船や橋の製造・加工といったようなものから、中程度ではたとえばブロンズ像(銅像)の制作、自動車のシャシやボディの製造、精巧なエンジン部品の加工・製作、アルミサッシの製造、金属製鍋の製造、小さなものでは指輪・ペンダント等々の装身具の製作やリフォーム、マイクロネジの製造、などといったものもある。そして各領域ごとの独特の技能・工程・道具がある。例えば中世の(またその伝統を受け継ぐ近・現代の)熟練の刀鍛冶はふいご・炭・槌などを用い玉鋼を鍛錬し成形し、焼入れ・焼もどし・焼なましなどの一連の熱処理を行い、研師はその刃をとぎ、また例えば近・現代のジュエリー工房では職人が金・銀・プラチナ等々の合金をガスバーナーややすりやペンチやはんだごてなどといった道具を用いて、美的感覚に配慮した細かな加工を手作業で行い、一方で現代の自動車工場では自動化された製造ラインの中で、毎日大量に、ロール状の鋼板を巨大なプレス機械に送り込み数千トンもの圧力で打ち抜いたり成形するなどして自動車のボディーのパーツを作り溶接ロボットにそれをつなぎ合わせる作業をさせていたり、また例えば精密な金属部品加工を行う工場や研究所等では工員やエンジニアや研究員などが、ただひとつの部品を作るために、コンピュータで数値制御された工作機械を用いて、切削ビットを自動交換させつつ、アルミのブロックを削る、といったように、ひとつひとつの領域ごとに、さまざまな技能・工程・道具で金属加工がおこなわれているのである。→#職人・専門家、#分類
歴史
[編集]先史時代
[編集]金属加工は先史時代にまで遡る。金属加工がいつどこで始まったのか正確にはわかっていない。最初期のテクノロジーは一時的で局所的なもので、長期に渡って証拠を残せるような規模ではなかった。金属に関する重要な進歩は、火と金属を結びつけたことだった。誰がいつどこでそれを実行したのかは不明だが、古代エジプト文明は金を扱うようになった最初の文明の1つとされている。
金属を扱うのに常に火を必要としたわけではない。アイザック・アシモフは「最初の金属」は金だったのではないかと考えた[1]。その根拠は、金が化学的に安定していて純金の塊として見つかることが多いという点である。言い換えれば、金は希少なものではあるが、見つかるときは事実上常に金属の形で見つかる。他の金属は隕石などでない限り、金属そのままの形で自然界に産することはめったにない。金以外のほとんどの金属は鉱石や鉱物を含む岩石の形で存在しており、そこから金属を取り出すには熱を加えるなどの工程を必要とする。金の別の特徴は、金の塊を見つけるには特別なテクノロジーが不要で目さえあればよく、それを加工するのも金床とハンマーがあればよいという点である。テクノロジーとしては石のハンマーと石の金床で十分だった。これは金の持つ可鍛性と延性のおかげである。先史時代の道具は石や骨や木で出来ており、そういった道具でも金を加工するのに十分だった。
ある時点で鉱石に熱を加えれば金属を取り出せることが判明し、銅やスズや鉛を多く含む岩石に需要が生じるようになった。それらの鉱石は発見されればどこであっても採掘された。古代の鉱山の痕跡は中東の至るところで見つかっている[2]。南アジアのメヘルガルでは、紀元前7000年から紀元前3300年にかけて金属加工が行われていた[3]。金属加工は紀元前6000年ごろ、中東で銅の精錬が一般化したことで本格化した。
古代人の7種の金属
[編集]古代人は7種類の金属を知っていた。以下にそれらを酸化還元電位の低いほうから順に挙げる。
酸化還元電位が低いほど鉱石から金属を取り出し易く、高いほど難しいので、金属加工の歴史を考える上で重要である。見ての通り、金の酸化還元電位は極めて低く、鉄の酸化還元電位は他に比べてずっと高い。金がそのままの形で産することが多いのも、酸化還元電位が低いおかげである。金塊は純金に近く、そのまま加工することができる。
-
紀元前2200~1700年ころに加工されたと推定されている、金製の品物。
-
ミケーネの遺跡で見つかったアガメムノンのマスク。(紀元前1550~1500年ころに制作)
-
「ツタンカーメンの黄金マスク」。黄金を材料にしてつくられている。(紀元前1323年)
-
プスセンネス1世(紀元前1039 - 991年ころ在位)の墓から見つかった葬儀用杯。左が銀製。中央が銀と金。右が金製。
-
銀の器。鳥の模様を加工。紀元前5世紀ころ。
-
古代ギリシアのテトラドラクマ。(写真は紀元前454-404年ころのもの)
-
本体が銀製で把手が青銅製の水差し(紀元前400年ころ)
銅、青銅、鉄の時代
[編集]- 銅
- 銅鉱石とスズ鉱石は比較的豊富にあり、金属加工の歴史の中で金の次に重要となった。銅鉱石を熱することで銅が豊富に生産されるようになった。銅は装飾品や簡単な道具に使われたが、銅単独では硬さを要求される刃物などの道具には不向きだった。
- 青銅
- ある時点で溶けた銅にスズを加えるという技法が生まれ、青銅が誕生した。青銅は銅とスズの合金である。青銅は純粋な銅に比べて硬く、刃物に加工できるという重要な利点があった。鉄の精錬が可能となるまでは青銅が最も進んだ金属として道具や武器に使われた(詳しくは青銅器時代を参照)。
- 中東以外でも同様の素材の発見と進歩が世界中で見られる。中国やイングランドでは銅単独の時代は非常に短く、すぐに青銅器時代に突入している。日本では青銅と鉄がほぼ同時期に使われ始めた。アメリカ大陸では事情が異なる。アメリカ大陸では金属は知られていたが、それを道具や武器に使うようになったのはヨーロッパ人が新大陸を発見してからのことである。それまでアメリカ大陸では金属はほとんど装飾品や芸術品に使われていた。
- 紀元前2700年ごろ、原料が入手可能な世界各地で青銅の生産が行われるようになっていた。
- 鉄
- その後、鉄の精錬が始まる。鉄は道具や武器の重要な原料として使われ始め、鉄器時代が到来する。
- 古代エジプト、古代インド、古代イスラエル、北米のマヤ文明など世界各地の古代文明で、希少な金属に独特の価値が付加されるようになっていった。場合によっては、貴金属の所有・分配・交易に規制をかけることもあった。このころの金属加工職人は鉄や鉄合金で武器を作るだけでなく、鉄以外の貴金属で装飾品や宗教用の器物などの制作も行った。それらの技能は時と共に高度になっていった。そのような技能を持つ職人は鍛冶屋、錬金術師などと呼ばれ、世界中に存在した。例えば粒金技法は、古くから世界各地の古代文化で見られる。
- 時と共に金属製品は一般化していき、高度化していった。金属の重要性が増すと同時に金属を入手し加工することへの需要も高まっていった。金属鉱脈を探す技能も登場し、金属加工の職人はさらに知識を蓄えていく。それらの職人は社会的にも重視されるようになっていった。金属とそれを加工する職人を入手した文明は大いに栄えることになった。
今日
[編集]
金属加工は貴金属から装飾品を作るだけでなく、様々な産業の基盤となっており、交通機関も金属加工に依存している。金属がなければ国際的な物流も今のような規模では行えない。
道具
[編集]日本の伝統的工具
[編集]![]() | この節の加筆が望まれています。 |
けがき針、槌(ハンマー)、均らし(フラッター)、鋸(ソウ)、鋏(直刃・えぐり刃・やなぎ刃)、鑢(丸・半丸・平・角)
近代的工具
[編集]

旋盤、ディスクグラインダー(グラインダー)など。レーザー加工(切断、溶接)もある。
職人・専門家
[編集]かつては鍛冶屋などと言う呼称も使われていた。鉄工所は、鉄という字が含まれているが、鉄に限らず広く金属類を加工することを請け負っている。 現在では、プレス職人、溶接工など、細分化された名称が主として用いられている。
分類
[編集]

金属加工は、「成形」、「切削」、「接合」に分けられ、それぞれに様々な工程がある。
材質 | |||||||||
---|---|---|---|---|---|---|---|---|---|
工程 | 鉄 | 鋼 | アルミニウム | 銅 | マグネシウム | ニッケル | 超硬合金 | チタン | 亜鉛 |
砂型鋳造 | ○ | ○ | ○ | ○ | ○ | ○ | △ | ||
金型鋳造 | ○ | △ | ○ | △ | ○ | △ | △ | ||
ダイカスト | ○ | △ | ○ | ○ | |||||
インベストメント鋳造 | ○ | ○ | ○ | △ | △ | ||||
型鍛造 | ○ | △ | △ | △ | △ | △ | △ | ||
押出成形 | △ | ○ | ○ | ○ | △ | △ | △ | ||
冷間圧造 | ○ | ○ | ○ | △ | |||||
プレス加工と絞り加工 | ○ | ○ | ○ | △ | ○ | △ | △ | ||
ねじ切り | △ | ○ | ○ | ○ | △ | ○ | △ | △ | △ |
粉末冶金 | ○ | ○ | △ | ○ | △ | ○ | △ | ||
凡例: ○ = よく行われる、△ = 若干困難を伴う、空白 = あまり推奨できない |
いずれの場合も、最終的な製品に合わせて原料となる金属材の寸法を計測し、レイアウトを決める必要がある。デザインやパターンを金属材に転写する工程を Marking out(en) という。大量生産ではこの工程は省略されるが、個人が金属加工する場合には必須である。
ノギスは2地点間の距離を正確に計測する道具で、0.1mmから0.01mmといった精度で計測できる。それほど精密さを要求されない用途では普通のメジャーもよく使われる。
成形加工
[編集]成形加工は、金属材の一部を除去することなく変形させる工程である。成形には熱や圧力、機械力などを使う。他の加工法にくらべ生産性が格段に高い。これらに用いる金型・工具等は金属同士の衝撃や高温にさらされるため、ほとんどが鉄鋼材料の一種である強固な工具鋼で製造される。
鋳造
[編集]
鋳造は熔解した金属を型に注ぎ、機械的な力を加えずに単にそれが冷却することで特定の形状にする。鋳造には以下のようなものがある。
塑性加工
[編集]
塑性加工とは、熱や圧力などを使って金属材を塑性変形させ、成形することをいう。歴史的には鍛冶屋のやっていたことが塑性加工と鋳造にあたるが、今では産業化されている。
板金成形
[編集]常温で機械力を加えることで成形する技法を指す。

切削加工
[編集]
切削加工は金属材から最終的な形状に不要な部分を除去することで最終的な製品の形に近づける各種工程の集まりである。切削加工によって生まれるのは、最終的な金属の部品や製品と金属屑である。木工で言えば、おが屑や木片が生じるのと同じである。金属の切削加工で出る屑も、削り屑と切断された金属片である。切削加工の多くは、削り屑を生じる何種類かの機械加工に分類される。酸水素ガストーチなどを使った溶接技法で金属を切断する溶断加工もあるが、これは機械加工ではない。他にもいくつか特殊な化学的切削加工がある。
金属に穴を開ける穿孔加工は削り屑を生じる加工工程の一例である。ガス溶接トーチを使って鋼板を溶断するのは溶断加工の一例である。化学的切削加工とは、化学薬品を使ってマスキングとエッチングを行うなどの技法である。
金属を切断する技法は様々である。以下に一部を挙げる。
- 人力の技法: 鋸、鑿、金切り鋏
- 機械加工: 旋盤、フライス盤、ドリル、グラインダー、切断機
- 溶断加工: レーザーによる切断、ガス溶接トーチによる切断、プラズマ切断
- 侵食加工: ウォータージェット、放電加工、エッチング
切削時には刃先や切断面に多大な摩擦熱が生じるため、切削油や冷却材が必須である。冷却材は一般に切削対象や道具の表面に広範囲に吹きつけ、温度を低下させることで道具の過度の摩滅を防ぐ。冷却材による冷却方法には様々なものがある。
機械加工
[編集]
機械加工は、金属などの素材から最終形状に不要な部分を除去することで複雑な形状を作る加工技術である。一般にフライスなどの工具と作業台から成るフライス盤という工作機械を使用する。フライスは回転切削(ミーリング)工具であり、作業台は複数の方向に移動可能である(通常X軸とY軸方向の2次元の動きをする)。回転工具はZ軸方向に動く。作業台全体を持ち上げることもできる。このような工作機械は手動操作も可能だが、CNC(コンピュータ数値制御)も可能である。様々な複雑な作業が可能で、溝削り、平削り、穴あけ、ねじ切り、リューターによる加工などがある。主軸の方向によって、立フライス盤と横フライス盤に分けられる。
複雑な3次元形状のものを製作でき、設計図からX, Y, Z軸の座標をCNCマシンに入れてやると、必要な作業を実行する。フライス盤は様々な3次元形状を作ることができるが、場合によっては加工対象物をX, Y, Z軸で回転させる必要がある。公差は1インチの数千分の1程度で、機械によって異なる。
刃先と加工対象物を冷却しておくために冷却剤が使われる。多くの場合冷却剤はホースから直接刃先と加工対象物に吹き付けられる。冷却剤の噴射はユーザーが制御する場合と機械が自動制御する場合がある。
アルミニウムからステンレス鋼まで様々な素材が加工可能である。ただし素材によって切削可能速度に違いがある。硬い素材では切削速度は遅い。柔らかい素材では一般に切削速度が速くなる。
フライス盤を使用することで様々な工程コストが付加される。まず、刃先の摩滅を防ぐために冷却剤の噴射が欠かせない。また、ある程度使った刃先は交換する必要がある。加工にかかる時間もコストに大きく影響する。複雑な部品の製作には時間がかかるが、単純な部品なら短時間でできる。加工時間の差は製品全体の完成までにかかる時間にも影響を及ぼす。
工作機械では安全性が重要である。刃先は高速回転しており作業員が接触すると危険である。また、加工時に出る切削屑(せっさくくず)(業界では、切り粉(きりこ)と呼ぶ)は加工で高温かつ鋭利になっていて皮膚に触れると危険である。CNCでは作業員が刃先や切り粉に近づく必要がないため、安全性が高い。
旋盤加工
[編集]
旋盤加工(ターニング)は、1点を削る工具を使って円筒状の表面を作り出す切削加工である。対象物を1つの軸を中心に回転させ、軸に対して垂直に、または軸方向に工具を接近させて削っていく。回転軸に対して垂直な面を削りだすことを「面削り (facing)」と呼ぶ。軸に対して放射状の方向からの切削と軸方向の切削を組み合わせて表面を削りだすことを「プロファイル加工 (profiling)」と呼ぶ[5]。
旋盤は工作機械の一種で、ブロック状または円筒状の素材を回転させ、研磨工具や切削工具を使い、回転軸を中心として対称な形状の物体を作る。例えば燭台、テーブルなどの脚、ボウル、野球のバット、クランクシャフト、カムシャフト、軸受の台などの形状を作ることができる。
旋盤は、主軸台、往復台、心押し台の3つの部分から成る。主軸台の主軸には加工対象を固定するチャック装置があり、3つから4つの爪で物体をしっかり挟む。主軸を高速で回転させることで、対象物を切削するエネルギーを与える。古くは天井からベルトで動力を伝達していたが、最近の旋盤は電動機を使っているものが多い。加工対象物は主軸の先に回転軸方向に設置される。往復台は回転軸方向に移動可能な台で、その上の横送り台で回転軸に対して直交する方向に移動可能となっている。その上の刃物台にバイトという切削工具を固定する。往復台を回転する加工対象物の周囲で移動させることで切削工具が対象物の切削を行い、必要な形状に切削していく。心押し台は回転軸方向に移動可能で、必要な位置に固定できる。センタと呼ばれる工具で加工対象物を主軸台の反対側から支えることができ、切削工具で対象物の回転軸に対してなんらかの加工を施すこともできる。
旋盤では他に次のような加工ができる[5]。
- 面取り: 円筒の角の部分を削る。
- 突切り: 軸に対して工具を放射方向から軸に向けていき、部品の一方の端を切り離す。
- ねじ切り: 対象物にねじ(雄ネジまたは雌ネジ)を切る。
- 中ぐり: 回転軸に開けた穴を大きくする。
- 穴あけ: 対象物の軸にドリルで穴を開ける。
- ローレット切り: 手で握る部分を意図して一定の斜交パターンを表面につける。
最近のCNC旋盤では独自に駆動された工具を使うこともでき、その場合は対象物自体は回転させない。そのため、最近のCNC旋盤は単なる回転体以外の様々な3次元形状も作ることができる。
旋盤加工の対象とする素材は比較的柔らかい金属だが、硬い金属でも切削に時間がかかるだけで不可能ではない。
バイトの素材は切削対象の金属より硬くなければならない。生産性は対象の素材の種類とそれに対して可能な切削速度で決まる。また、最終的な形状が複雑なほど時間がかかる。
ねじ切り加工
[編集]
ねじ切り工程には様々なものがある。ねじ切りダイスを使った方法、専用のねじ切り盤を使う方法、ねじ転造盤を使う方法などがある。タップはドリルで開けた穴の内側に雌ネジを切るのに使われ、ねじ切りダイスは丸い棒に雄ネジを切るのに使われる。
研削加工
[編集]
研削加工は金属素材を研磨する工程である。工作機械の一種であるグラインダーで、軽く切削することで非常に滑らかな表面仕上げをしたり、砥石車を使って高精度な仕上げをする。砥石車には様々な大きさのものがあり、石やダイヤモンドや無機化合物でできている。
最も単純なグラインダーとして、金属部品のバリ取りに使われるベンチグラインダーや小型アングルグラインダーがある。
グラインダーはテクノロジーの進化とともに大きさと複雑さが増していった。手動の砥石車から、ジェットタービン製作に使われる毎分3万回転のCNCグラインダーまで様々なものがある。
グラインダーで仕上げをするには、対象とする金属より硬くなければならない。中にはCNCの軸の位置決めに使われるガラススケールの製造に使われるグラインダーもある。一般にある機械の部品を製造する機械は、対象機械の10倍の正確さでなければならない。
かつての砥石車は表面仕上げに使える場面が限られていた。現代の砥石車は工業用ダイヤモンドなどの人工コーティング材(立方晶窒化ホウ素)を使っており、利用できる用途が広がっている。
現代ではCNC制御を含む進んだ研削加工があり、高精度に材質を削ることができ、航空宇宙用途や高精度部品の大量生産にも使えるようになっている。
やすりがけ加工
[編集]
やすりがけ加工は、やすりを使って研磨と切断を行う加工技法である。工作機械が登場する以前は相対的に精密な小型部品を作るのに使われていた。特に平らな表面仕上げを得意とする。かつて熟練した機械工はやすりで微妙な調整を行うことができ、それが技能の証明にもなっていた。やすりがけは標準的生産技術としてはめったに使われないが、バリ取りにはよく使われている。
その他
[編集]金属に空いた穴の内面を様々に切削するブローチ加工がある。電子ビーム加工機 (EBM) は高速な電子を金属材に当て、金属を微細に気化させて加工する。超音波加工機は超音波を使うもので、非常に硬い素材や脆い素材に適している。
接合加工
[編集]
溶接
[編集]溶接は金属材同士を金属または熱可塑性物質で溶融・一体化させる工程である。通常、金属材の接合部を溶かし充填材を付加することで溶融物質のプールを形成し、それが冷却することで一体化する。熱と同時に圧力を加えて溶融させることもある。
溶接のエネルギー源は様々であり、ガスの火、電弧、レーザー、電子ビーム、摩擦熱、超音波などがある。工場で行うのが一般的だが、屋外、水中、宇宙空間などでも溶接は行われている。どんな環境であっても溶接は危険な作業であり、やけどや感電、有毒ガスの発生、紫外線への当たりすぎなどに注意が必要である。
ろう付け
[編集]ろう付けは充填金属を溶かし、毛細管現象を利用して金属材の接合部に流し込んで、金属材同士を接合する。充填材は冶金的に金属材と反応し、金属材の細部に侵入して凝固することで強固な接合を実現する。溶接とは異なり、金属材自体は融けない。はんだ付けとよく似ているが、ろう付けの温度は450℃以上である。溶接に比べると金属材に与える熱応力が小さく、合金の性質を変えにくいため、溶接よりも展延性が優れている。
トーチろう付け、抵抗ろう付け、炉内ろう付け、拡散ろう付け、誘導加熱ろう付けなどの技法がある。
はんだ付け
[編集]
はんだ付けは450℃以下の温度で行う接合工程である。ろう付けと基本原理は同じだが、充填材が異なり温度がさらに低い。そのため金属材との冶金的反応は最小限であり、接合は弱いものとなる。
関連する加工
[編集]以下に挙げる加工工程は本質的には金属加工とは言えないが、金属加工工程の前後に実施されることが多い。
熱処理
[編集]金属は熱処理することで、強さ、展延性、剛性、硬度、耐腐食性などの特性を変化させることができる。一般的な熱処理工程として、焼きなまし、析出強化、焼入れ、焼き戻しがある。「焼きなまし」は金属を軟化させる。「焼入れ」は鋼などを硬化させる。「焼き戻し」は焼入れで硬化した鋼に対してじん性を強化する(衝撃への脆さを改善する)。
熱処理と物理的な力を組み合わせることで金属の性質の改善を行うことが多い。これらの技法は特殊鋼や超合金やチタン合金でも共通である。
めっき
[編集]金属材の表面処理として電気めっきがよく行われる。金、銀、クロム、亜鉛などの薄い膜を金属材表面に形成する。腐食を防ぎ、見た目も改善される。
溶射
[編集]溶射はめっきとは別の表面仕上げ技法で、電気めっきよりも高温特性がよい場合が多い。
金属加工が特に盛んな街、市
[編集]脚注
[編集]- ^ Asimov, Isaac: "The Solar System and Back", page 151 ff. Doubleday and Company,Inc. 1969.
- ^ Percy Knauth et al.: "The Emergence of Man, The Metalsmiths", page 10-11 ff. Time-Life Books, 1974.
- ^ Possehl, Gregory L. (1996). Mehrgarh in Oxford Companion to Archaeology, edited by Brian Fagan. Oxford University Press.
- ^ Degarmo, E. Paul; Black, J T.; Kohser, Ronald A. (2003), Materials and Processes in Manufacturing (9th ed.), Wiley, p. 183, ISBN 0-471-65653-4
- ^ a b Schneider, George. Turning Tools and Operations, American Machinist, January 2010
関連書
[編集]- 田中和明『図解入門 よくわかる最新金属の基本と仕組み―性質、加工、生産、表面処理の基礎知識 初歩から学ぶ金属の常識』秀和システム, 2006, ISBN 4798014869
- 木村尚『粉末冶金―その歴史と発展』アグネ技術センター, 1999, ISBN 4900041742
- 大和久重雄『熱処理のおはなし』日本規格協会, 1982, ISBN 4542901084
- 山下恒雄『鍛金の実際―美しい形をつくり出す手と槌の技法』美術出版社, 1978, ASIN B000J8OEKU
- 香取正彦『金工の伝統技法』理工学社, 1986, ISBN 4844585509